The ideas of living in the digital simulation of the world or using virtual prototypes of people presented in legendary science-fiction movies The Matrix and Avatar have partially become a reality. Engineers can now create virtual models of objects, processes and large systems thanks to digital twin technology. It may sound surprising, but you can already find digital twins implemented across many sectors, and scientists believe that digital versions of humans will also appear soon.
Let’s learn more about this technology since it’s going to become a part of our everyday life.
What Is a Digital Twin?
A digital twin is a virtual prototype of a real-life object or product that can monitor, analyze and improve its performance.
Though the digital twin concept originated in 2002, it could be implemented only in the 2010s when cloud computing, big data, the Internet of Things and artificial intelligence started to gain traction.
Leverage the latest IoT technologies with our expert team and get powerful IoT solution for your business.
A digital representation of a physical object is “live” and dynamic, meaning that it is updated every time its real-world twin undergoes changes. It can also learn, absorbing the knowledge from people, machines and the environment it exists in.
The model is created with the help of visualization technologies (3D modeling, AR) that display data collected from embedded sensors and IoT devices, which is then analyzed by machine learning algorithms and big data analytics.

Types of Digital Twins
Virtual models are divided into three categories depending on what they simulate.
Product twins simulate separate objects. For instance, manufacturers use a virtual prototype of a certain product before setting up a production line to analyze how it will perform under various conditions, and what issues may occur. This allows them to make necessary adjustments and create a more efficient design of goods. Afterward, product twins can be used to control product performance in the physical world.
Process twins are responsible for the simulation of processes; for example, manufacturing processes. In a virtual environment, you can create various scenarios of a production process to see what will happen in different situations. This allows companies to develop the most efficient production methodology. You can further optimize the process using product twins that correspond with every piece of equipment involved. This helps companies perform preventative maintenance, avoiding costly downtimes. Manufacturing operations are made safer, faster and more efficient.
System twins are copies of entire systems (e.g., a factory). They collect massive amounts of operational data produced by devices and products in the system, gain insights and create new business horizons to optimize all the processes and support the system’s integrity.
How Are Digital Twins Created
Data collection. First of all, researchers have to aggregate a variety of data about an asset: physical properties, appearance, behavior under certain conditions, cooperation with other assets and more.
Modeling. Using the gathered data and modeling software, engineers create a mathematical model that accurately reflects all the specifics of its real-world counterpart. The model has an identical appearance to the corresponding object, including all minor details, and behaves in the same way as the original object. AR, virtual reality and 3D technologies help with visualization.
Integration. Finally, you need to integrate your asset with its digital model to enable continuous monitoring in real time. To do so, the asset is equipped with sensors and tracking devices that can transmit data to an IoT platform where it will be visualized and analyzed.
In a nutshell, engineers build a virtual copy of a physical product using computer modeling techniques. Then, sensors are connected to the object to collect a variety of data in online mode. The data is uploaded to the cloud-based IoT platform for processing, where AI or ML algorithms analyze it and determine possible scenarios. Thus, we get a working digital twin model.
How Does a Digital Twin Work?
Digital twins can have various complexities, depending on requirements and the needed amount of information to be processed. So, when creating a digital twin, you should decide on its functions: whether it will just monitor the prototype, or alert you about abnormalities and suggest solutions based on advanced data analytics.
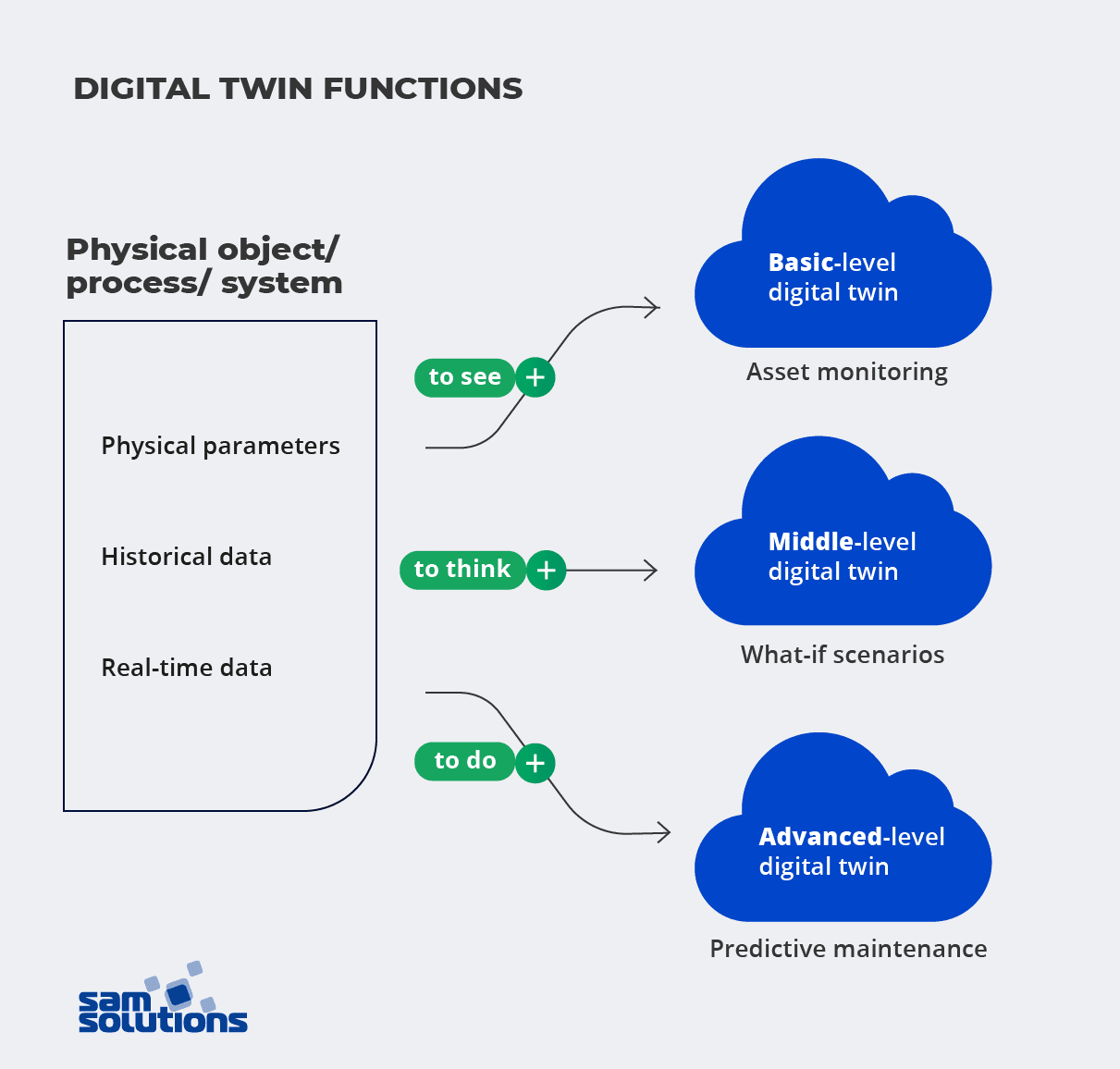
Digital Twin Functions
In general, virtual models can be used to monitor, analyze and optimize the performance of their physical prototypes. Figuratively, we can distinguish three groups of their functions:
- To see — basic-level digital twins perform monitoring, enabled by the data obtained from sensors and devices and a software program that visualizes the situation.
- To think — middle-level DTs equipped with what-if models can change operational settings in order to find the best asset or process configuration.
- To do — advanced-level digital twins utilize intelligent algorithms to learn from collected data, detect issues, find several possible solutions to each one and choose the most appropriate solution. They provide predictive maintenance.
When to Use Digital Twins
Virtual copies can be applied at all stages of product creation, including design, production, operation and disposal.
At the design stage, engineers create versions of a computer model for the product under development to assess and select possible technical solutions. Then, they select the most appropriate model, called the Digital Twin Prototype (DTP), which contains the information needed to describe and create physical versions of product instances.
At the production stage, the DTP helps achieve the required characteristics of the outcome.
At the operation stage, Digital Twin Instance (DTI) is used. This is a virtual copy of a specific sample of a product with which the twin remains associated throughout its lifecycle. Twins of this type are created on the basis of DTP and additionally contain information on the history of product manufacturing, the use of materials and components, statistics of failures, repairs, replacement of units and assembly, quality control, etc. DTI undergoes similar changes as its physical instance during its operation.
At the disposal stage, DTI is also used.
There is also the Digital Twin Aggregate (DTA) — an information management system that has access to numerous digital twins of a product family.
Why Is Digital Twin Technology Important?
The technology uses visualization techniques to allow users to see the inner problems of physical objects or processes without having to access them physically and to solve them with no health and safety risks. Digital twins also save time and money on design, testing, implementation and modification of products, systems and processes.
Challenges that Digital Twins Help Solve
The main challenge that digital twins help address is detecting issues before they occur. And digital twins perform this function in many industries. For example, virtual models are more effective than human workers in the diagnosis of equipment malfunctions, as they gather information about the state of spare parts from sensors in real time, allowing maintenance specialists to replace or fix them before serious damage occurs.
Benefits of Digital Twins
1. Streamlined Design
As a rule, a new product goes through multiple iterations before a working prototype appears. This process is very expensive because it requires a significant contribution of time and labor. Virtual modeling eliminates many issues at the design stage, which results in more seamless prototyping.
2. Cost Cutting
Digital twins make it possible to reduce defects during actual production and operation, allowing engineers to carry out all tests and simulations in the virtual environment. It is much easier, cheaper and faster to fix defects in the digital context than in the real world. Producers can eliminate almost all of the risks of the future output and make sure that the physical object will perform exactly as planned.
The technology also provides continuous remote maintenance that is also cost-effective for business, as fewer employees can be involved.
3. Reduced Time to Market
Half the battle for every company is getting to market faster than its competitors. But this problem usually occurs because of long iterations and the need for constant improvements.
When companies create products or services with virtual twin assistance, they can reduce time to market. The lifecycle of a product is performed in the digital environment where all improvements can be done much more quickly and easily. A virtual prototype verifies how its physical copy will behave in reality, thus optimizing the effectiveness and time of development. So, you can hit the market as soon as production begins.
4. Predictive Maintenance
One more essential benefit of digital twin technology is that it can solve many problems well in advance. This capability is called predictive maintenance.
Digital copies perform constant remote control of their physical prototypes gathering various state information via sensors. The analysis of the gathered data enables the prediction of possible breakdowns, e.g. if a spare part is nearly worn out and needs to be replaced. Human operators will get reports about issues and address them in a timely manner. If a spare part is replaced before it is broken, more serious damage and unnecessary downtime can be avoided, thus saving time and money.
5. Improved Customer Experience
With the help of digital twins, companies can prevent practically all potential issues, thus delivering error-free products and impeccable services to their clients and improving customer experience.
Industries Using Digital Twins
Practical use of digital twins is increasing steadily with more industries implementing data science and the Internet of Things into their operational processes.
Manufacturing
Currently, digital twin technology is more widely implemented in the manufacturing industry. Virtual copies of entire factories are created to ensure transparent production processes. Twins monitor operating conditions of equipment elements and machines (temperature, rotation rate, humidity, etc.), analyze historical and real-time data to optimize manufacturing operations, and send out alerts when maintenance work is needed. As a result, manufacturers enhance productivity, improve the quality of their goods and get higher profits.
Healthcare
Digital twins have high potential in healthcare. A range of DT medical applications include surgery assistance, diagnosis assistance, the monitoring of the entire clinic and the design of medical devices. Virtual modeling and simulation can be of great help when it comes to people’s health and lives.
Energy Sector
Power generation by fossil fuels or renewable sources involves complicated infrastructure and assets often located in remote areas. Digital twin technology ensures continuous monitoring and safe operation of such systems.
Wind farms
The US corporation General Electric was the first company to use digital twins. The technology was used to monitor wind aircraft engines and turbines and improve their efficiency. To date, the company has already created more than half a million virtual copies for a wide range of products, processes and systems.
Oil and gas industry
Engineers at energy and oil-producing companies leverage virtual replicas to control thousands of pipes in remote locations, even those hidden under the snow in Alaska. Siemens Energy created digital twins of its huge gas turbines to monitor their performance and run tests.
Smart Cities
3D digital twins of whole cities already exist, such as Virtual Singapore. These systems provide valuable insights that city authorities use to monitor, plan and improve social infrastructure, streamline logistics, inform citizens and, in general, enhance city life. Digital replicas aid construction projects and transportation companies to fit their processes into the density of large cities.
Space Exploration
The National Aeronautics and Space Administration (NASA) tests all the equipment first in a virtual environment. Devices are not manufactured physically until their digital counterparts satisfy all the required characteristics.
Our Experience
SaM Solutions has rich experience in providing end-to-end IoT services across industries such as smart homes, healthcare, logistics, manufacturing, retail, agriculture, infrastructure and smart assets management. Related services, including cloud computing, mobile app development and 3D visualization, ensure the basis for creating innovative digital projects.
Thank you for covering such an interesting topic. I’ve heard of digital twins before but haven’t thought that they are already widely used in practice. That’s impressive.
I guess that simulation of physical assets is the next frontier of today’s technology-driven world. So many mistakes can be avoided and so much money can be saved due to virtual copies.
Leveraging digital twin technology is a wise business decision across numerous sectors. With IoT enhancement, digital twins will also improve and impact better business outcomes.
I like the comprehensive explanation of the digital twin technology you’ve provided in this article. I’ve learned many useful facts, thank you!
The technology is very interesting, and its potential is enormous. I’m sure that many industries will enhance the efficiency and sustainability of their processes in the near future due to digital twins.
Thank you for this wonderful blog explaining in detail about the digital twin. The blog is written in a interesting and simple manner.
Great article. I want to add that digital twins of buildings are not only possible, they are fast becoming a reality – helping construction firms deliver projects on time and on budget, and helping building owners reduce running costs and the environmental footprint of the building.
Thank you, Mark, for your feedback, it’s much appreciated!
You are absolutely right, digital twins are of great help to the building industry.